BETTER, CLEANER HEAT USAGE
This work is focused on high-performance thermal management and waste heat recovery research for improved, i.e. cleaner and more efficient heat usage in energy conversion technologies.
IRP4 addresses two key challenges in power generation systems: a) the efficient management of heat and b) the emission of harmful pollutants, which is particularly problematic in fuel-based technologies such as diesel engine power plants or marine engines.
Regulations are increasingly stringent for these systems and a full understanding of the underlying phenomena is necessary to tackle this problem.
FEATURED RESEARCH
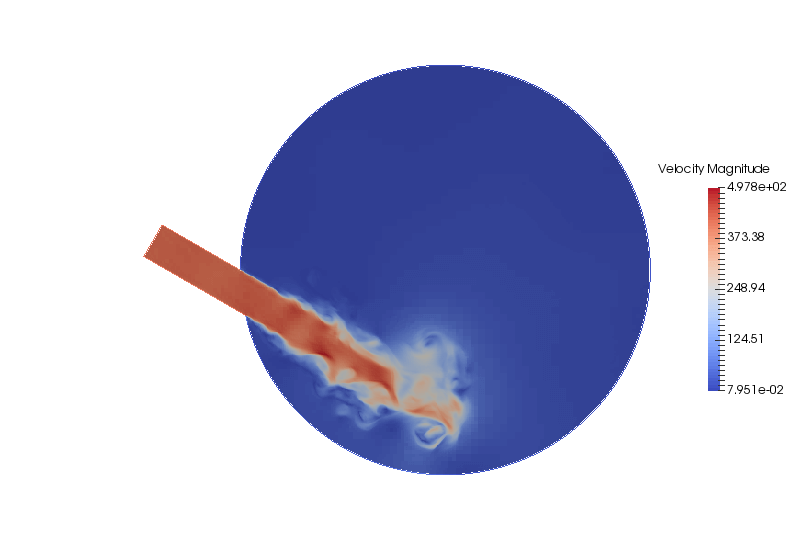
A new engine combustion chamber
A simulation of a marine-engine-like test configuration, with a constant-volume combustion chamber previously studied by Sulzer and
ETH Zürich, has been launched. In this configuration, a heavy fuel oil spray injected in a swirl flow, at marine-engine pressures and temperatures, evaporates and then autoignites. The experimental dataset includes pressure vs time signals and spray imaging and will be used for model validation. The air enters the combustion chamber at an angle, which will create the needed swirl to promote
spray dispersion and efficient fuel mixing. In the future, such simulations will also be performed for reciprocating marine engines for which a well-characterised set of experimental data exists.
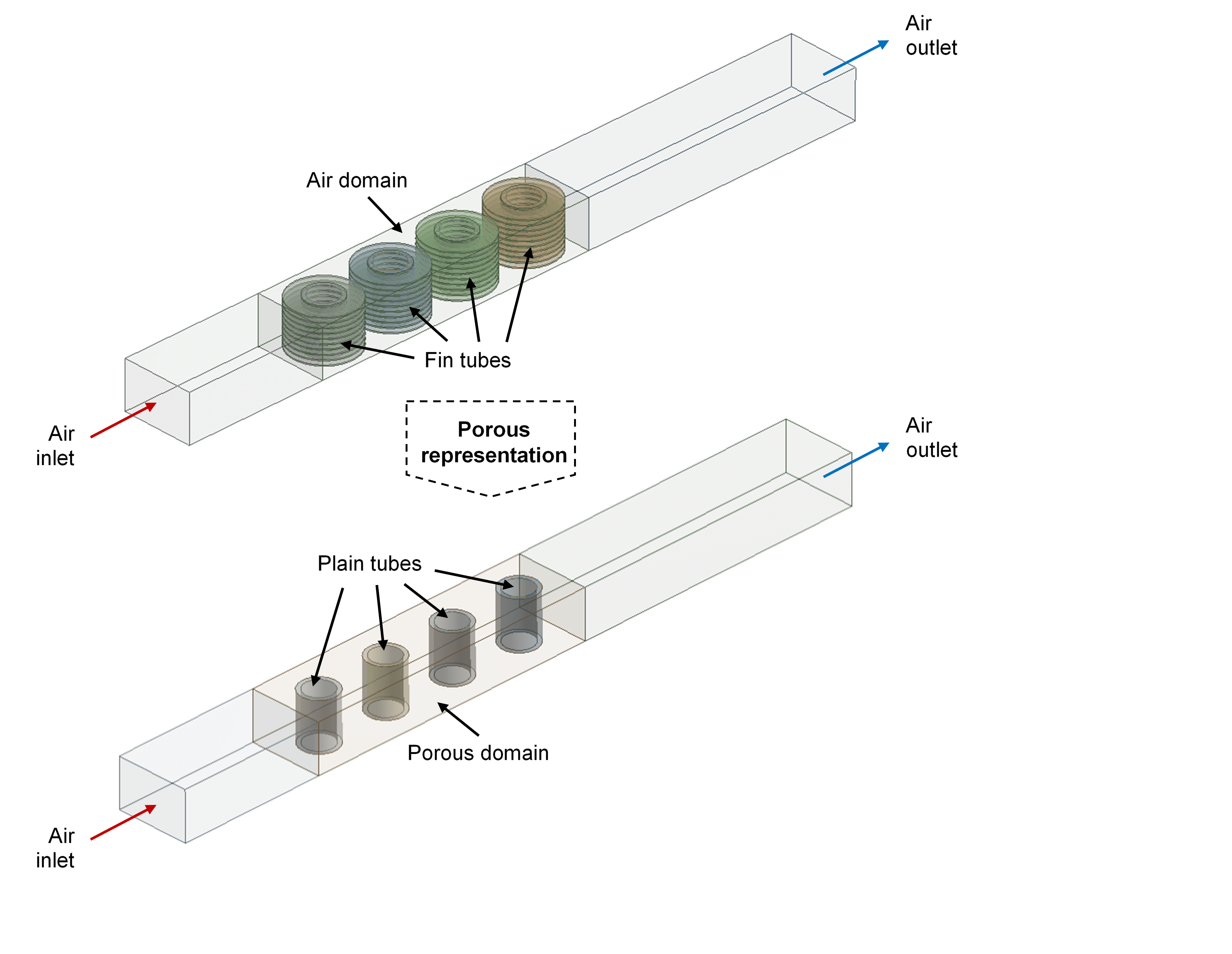
A high-efficiency heat exchanger
Researchers have been working on the development of a triplefluid heat exchanger, focusing on modelling of the air and fin region as porous media. The method of using porous approximation to represent the fin domain reduces the fin-tube heat exchanger to a plain-tube model.
This brings about a decrease in grid size, which leads to a drop in computational time and resources. However, simplifying the model does
not mean that accuracy of the solution has to be greatly compromised. Computational fluid dynamics simulation results show that the air-side pressure drop of the porous model has good agreement with the fin model. As a result, full scale simulations of the entire length of the heat exchanger can be carried out with this porous model without sacrificing accuracy.

Closed power cycles
An efficient turbocharger turbines benefits an engine in many aspects, for example lower backpressure and a better transient response. The turbine performance can be further improved by injecting the secondary flow through an injector over the turbine shroud. The secondary flow can effectively reduce the vortex separation on the suction side and reduce associated losses. Without affecting the original impeller design, the injection flow can be achieved by modifying only the turbine housing, which is cost effective. In order to find the injection design that maximises the turbine performance, eleven design parameters have been considered which control the circumferential area distribution, exit flow angles and flow velocities.